Blenders
As a tablet manufacturer, customers very well understand that blending practices influence tablet compression. Sometimes, it is observed that the hardness of the tablet does not match the hardness achieved at the R&D stage, even if other parameters like weight, thickness, disintegration time, etc match. Insufficient tablet hardness can lead to lamination or erosion of the tablet during the coating stage. And the answer lies in blending.
Ideally tumbling class blender is more common in tablet production. This blender works on diffusion and axial blending mixing mechanism.
Following are the different types of blenders Exenity can help you
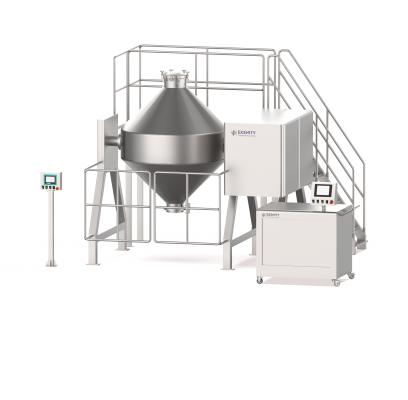
Conta/Bin Blender
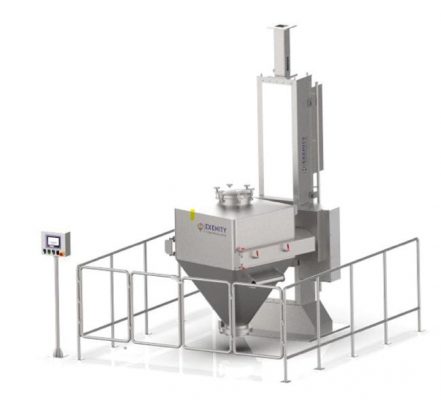
Bin blender is more prevalent in current practice as it reduces the transfer of material from one container to another after dry milling and blending and hence reducing dusting as well as handling.
The key differentiator of Exenity’s Bin Blender
- SS 316 L MOC with all supporting certificates
- Different capacity bins can be used
- Both clockwise and anti-clockwise rotation possible
- RPM managed using VFD, controlled from HMI
- Flameproof or ATEX construction (optional)
- Mirror finish for contact parts and matt finish for non-contact parts
- Full compliance to cGMP requirements
- Full compliance to 21 CRR Part 11 compliance (optional)
- Capacities from 100 L to 4000 L
Double Cone Blender
A double cone blender is suitable for blending granules and lubricants as well as it can be used for powders.
- Double cone blender works on axial as well as rotational mixing principles
- SS 316 L MOC with all supporting certificates
- RPM managed using VFD, controlled from HMI
- Flameproof or ATEX construction (optional)
- Mirror finish for contact parts and matt finish for non-contact parts
- Full compliance with cGMP requirements
- Full compliance to 21 CRR Part 11 compliance (optional)
- Machine offers a suitable protection structure to avoid any accident.
- Vacuum loading of granules/powders (optional)
- Discharge by gravity. Vacuum discharge can be offered as an option.
- Pneumatically operated butterfly valve (optional)
- Provision for WIP nozzles (optional)
- Stairs for inspection, in case of bigger volumes (optional)
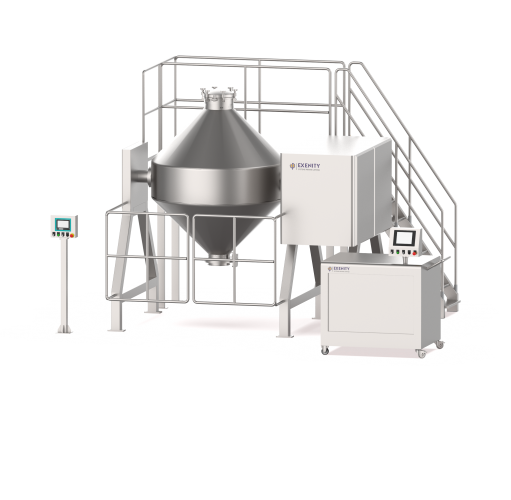
Octagonal Blender
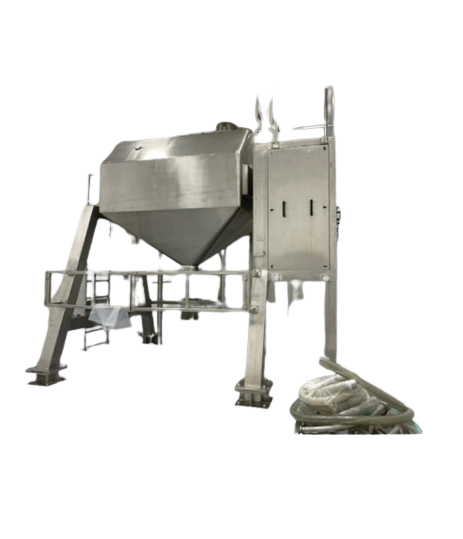
The octagonal blender works on a similar principle as that of a Double cone blender. Ger box is directly coupled and no belt or chains are used for power transmission.
- SS 316 L MOC with all supporting certificates
- RPM managed using VFD, controlled from HMI
- Flameproof or ATEX construction (optional)
- Mirror finish for contact parts and matt finish for non-contact parts
- Full compliance to cGMP requirements
- Full compliance to 21 CRR Part 11 compliance (optional)
- Machine offers a suitable protection structure to avoid any accident.
- Vacuum loading of granules/powders (optional)
- Discharge by gravity. Vacuum discharge can be offered as an option.
- Pneumatically operated butterfly valve (optional)
- Provision for WIP nozzles (optional)
V Blender
- Easy loading and unloading
- Can be loaded using vacuum transfer system
- No dead zones
- Easy to clean
- No sharp edges
- MOC is SS 316 L with certificates
- RPM managed using VFD, controlled from HMI
- Flameproof or ATEX construction (optional)
- Mirror finish for contact parts and matt finish for non-contact parts
- Full compliance to cGMP requirements
- Full compliance to 21 CRR Part 11 compliance (optional)
- Machine offers a suitable protection structure to avoid any accident.
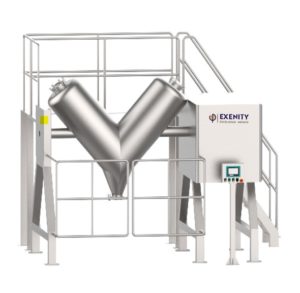